Heinrich Safety Pyramid: A Proven Framework for Accident Prevention in Indian Industries
Discover the Heinrich Safety Pyramid model for workplace accident prevention. Learn how the 1:29:300 ratio helps reduce industrial accidents through proactive safety management.
Introduction to the Heinrich Safety Pyramid
In the realm of industrial safety management, few models have stood the test of time like the Heinrich Safety Pyramid—also known as the Heinrich Triangle or Accident Ratio Model. This foundational framework, introduced by Herbert William Heinrich in the 1930s, continues to guide safety professionals worldwide in understanding and preventing workplace accidents.
For Indian industries facing increasing safety regulations and awareness, the Heinrich model provides a data-driven approach to accident prevention that can significantly reduce workplace incidents and improve overall safety culture.
What Is the Heinrich Safety Pyramid?
The Heinrich Safety Pyramid is built on comprehensive analysis of over 75,000 accident reports. Heinrich's groundbreaking research revealed a consistent statistical relationship between different levels of safety incidents:
The Heinrich Ratio
For every 1 major injury, there are:
- 29 minor injuries (requiring first aid)
- 300 near misses or unsafe acts
This 1:29:300 ratio demonstrates that serious incidents rarely occur in isolation. Instead, they are typically preceded by numerous unreported or unnoticed unsafe behaviors and conditions—making prevention both predictable and achievable.
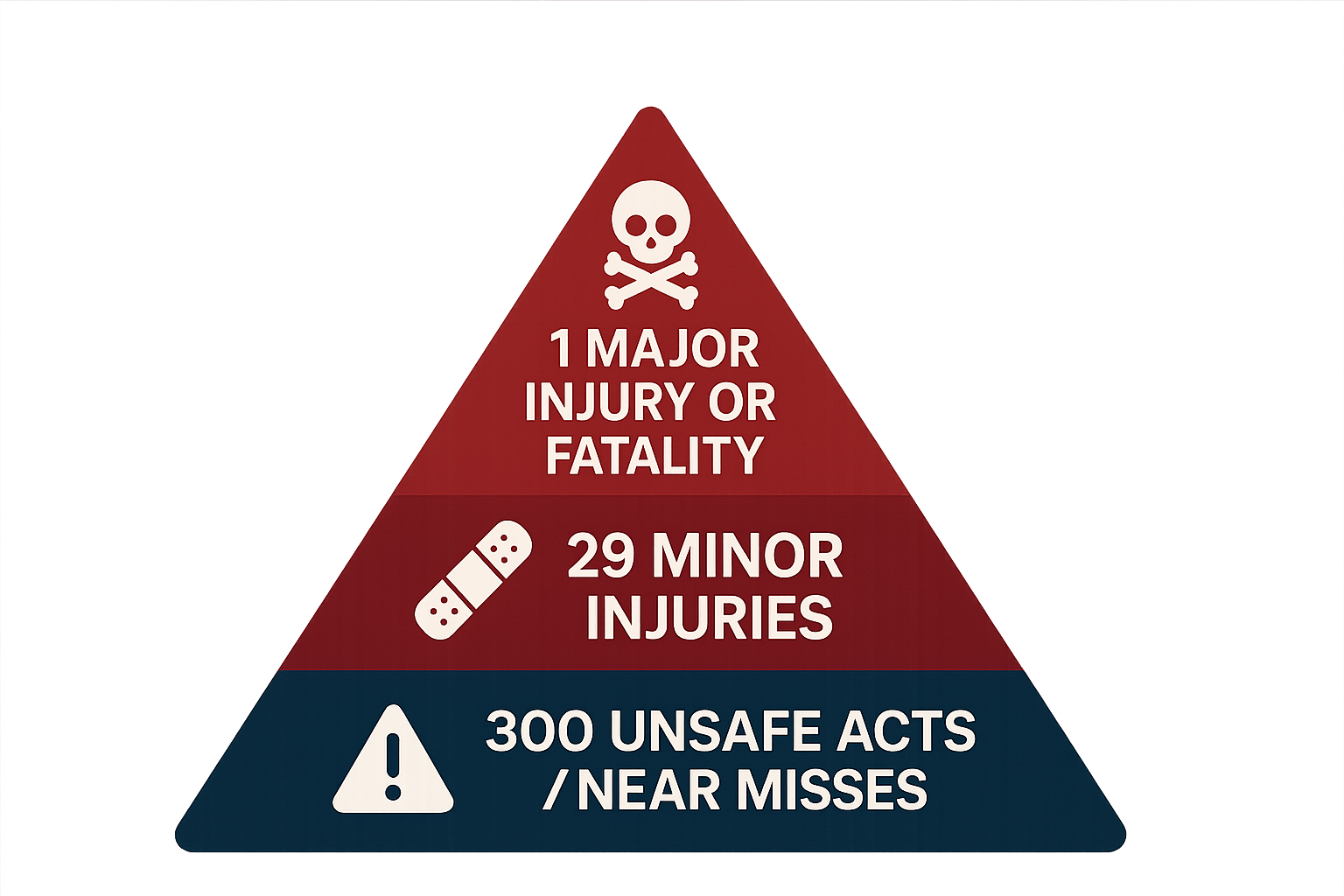
Figure 1: The Heinrich Safety Pyramid illustrating the relationship between major injuries, minor injuries, and near misses in workplace safety.
Core Principles of the Heinrich Model
1. Accidents Are Predictable and Preventable
Heinrich's research fundamentally changed how we view workplace accidents. Rather than random occurrences, most workplace accidents result from identifiable unsafe human behaviors and systemic issues. This means that by analyzing and addressing near misses and minor injuries, organizations can often prevent major injuries before they occur.
2. Unsafe Acts Are Leading Indicators
One of Heinrich's most significant findings was that 88% of all workplace accidents are caused by unsafe acts rather than unsafe conditions. This insight emphasizes the critical importance of:
- Employee behavior modification
- Comprehensive safety training programs
- Building a strong organizational safety culture
- Regular behavioral safety audits
3. Proactive Safety Reduces Serious Incidents
Rather than adopting a reactive approach that waits for major injuries to trigger action, the Heinrich model advocates for treating near misses and unsafe acts as early warning signals. This proactive stance enables organizations to implement corrective measures in real-time, preventing escalation to serious incidents.
Modern Applications in Indian Industries
While the original Heinrich ratios may vary across different industries and regions, the pyramid's preventive value remains as relevant today as it was nearly a century ago. Modern Indian safety systems successfully apply this model to:
Track Leading Indicators
Monitor and analyze unsafe acts, equipment misuse, and behavioral patterns before they escalate.
Behavioral Safety Programs
Develop comprehensive Behavioral-Based Safety (BBS) programs that focus on changing unsafe behaviors.
Root Cause Analysis
Strengthen incident investigation processes to identify and address underlying systemic issues.
Reporting Culture
Cultivate an environment where near misses are encouraged to be reported without fear of punishment.
Modern Evolution
Contemporary safety models have enhanced the original Heinrich pyramid by adding a fourth base layer for unsafe conditions or hazards identified without incidents, creating an even more comprehensive prevention framework.
Implementing the Heinrich Safety Pyramid in Your Workplace
Successfully applying the Heinrich approach requires systematic implementation across multiple organizational levels. Here's a comprehensive action plan:
Action Area | Description | Key Benefits |
---|---|---|
Incident Reporting System | Implement comprehensive systems to capture all near misses and minor incidents, not just recordable injuries | Early warning system for potential major incidents |
Root Cause Analysis | Investigate every incident thoroughly to identify underlying systemic and behavioral causes | Prevents recurrence and addresses systemic issues |
Behavioral Safety Audits | Conduct regular observations to identify and correct unsafe behaviors proactively | Reduces the 88% of accidents caused by unsafe acts |
Training Programs | Educate employees on hazard recognition, safety protocols, and the importance of reporting | Builds safety awareness and competency |
Safety Culture Development | Foster transparency, non-punitive reporting, and management commitment to safety | Encourages proactive safety participation |
Real-World Benefits for Indian Industries
Organizations implementing the Heinrich Safety Pyramid approach in India have reported significant improvements:
- Reduced Accident Rates: Up to 40% reduction in serious injuries
- Improved Compliance: Better adherence to IS standards and safety regulations
- Cost Savings: Lower insurance premiums and reduced downtime
- Enhanced Reputation: Improved stakeholder confidence and employee morale
- Operational Efficiency: Fewer disruptions and improved productivity
Getting Started: Your Heinrich Implementation Checklist
Implementation Steps
- Assessment: Evaluate current incident reporting and investigation processes
- System Setup: Implement comprehensive near-miss reporting systems
- Training: Educate all employees on the Heinrich model and reporting procedures
- Culture Change: Establish non-punitive reporting policies
- Monitoring: Track ratios and trends across all incident levels
- Continuous Improvement: Regular review and enhancement of safety systems
HSSPL: Your Partner in Heinrich Implementation
At Height Safety Systems Pvt. Ltd. (HSSPL), we understand the critical importance of proactive safety management. Our comprehensive range of fall protection equipment and safety systems are designed to support your Heinrich Safety Pyramid implementation:
- Fall Arrest Systems - Prevent major injuries at height
- Horizontal & Vertical Lifeline Systems - Comprehensive protection infrastructure
- Personal Protective Equipment - Quality safety gear for all workers
- Safety Training & Consultation - Expert guidance on safety implementation
Conclusion
The Heinrich Safety Pyramid remains one of the most valuable tools in industrial safety management. By understanding and applying the 1:29:300 ratio, Indian industries can transform their safety culture from reactive to proactive, potentially preventing hundreds of incidents for every major injury avoided.
Remember, every near miss is an opportunity to prevent a serious accident. Start implementing the Heinrich approach today, and build a safer tomorrow for your workforce.
Ready to Enhance Your Safety Program?
Contact HSSPL today to learn how our safety solutions can support your Heinrich Safety Pyramid implementation. Our experts are ready to help you build a comprehensive accident prevention program tailored to your industry needs.
Related Safety Articles
Fall Protection Compliance Guide
Complete guide to safety standards and regulations in India.
PPE Selection Guide
Essential personal protective equipment for construction sites.
Monsoon Safety Essentials
Critical safety equipment for monsoon season construction work.