Overhead Lifeline Systems: Complete Installation and Safety Guide
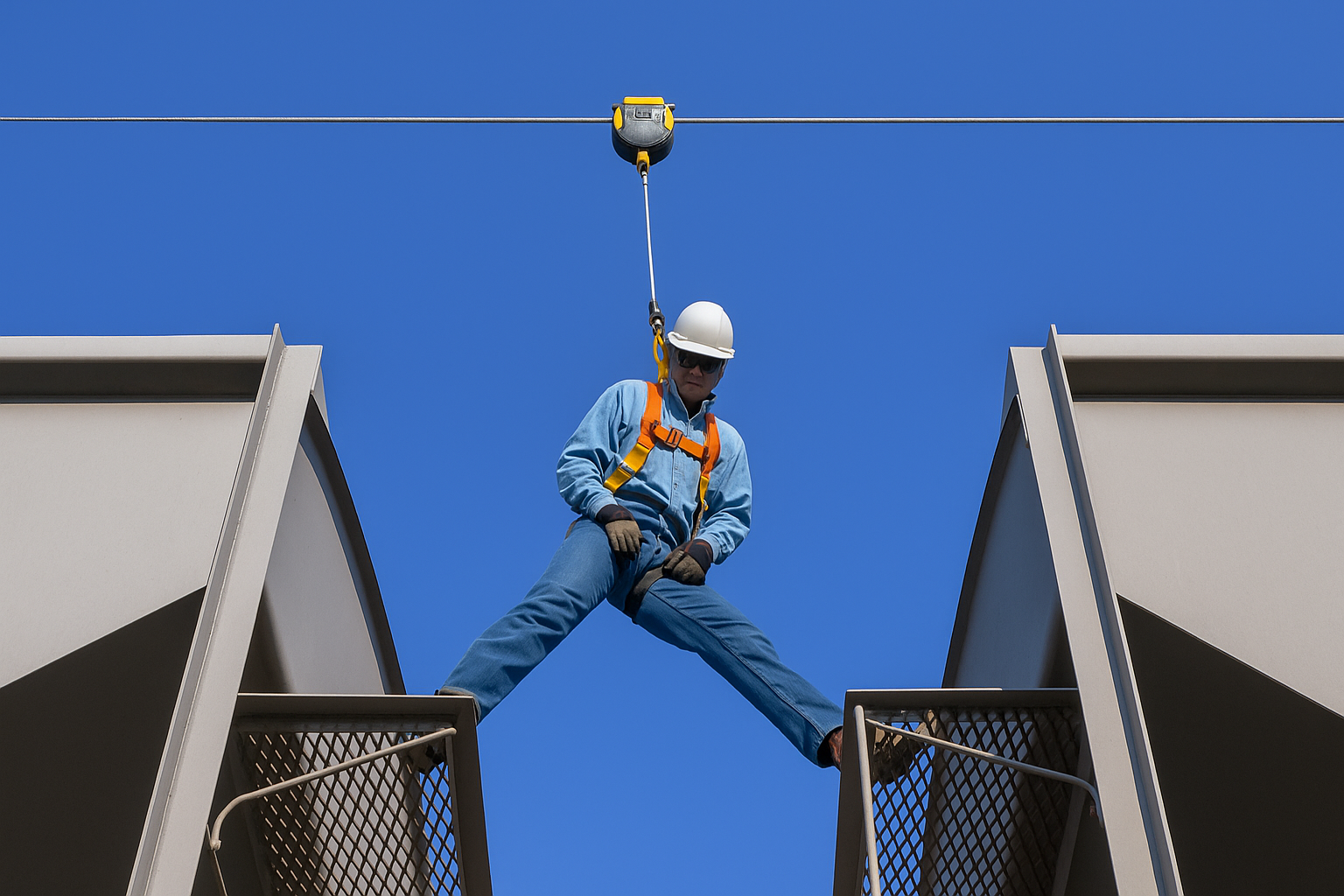
Overhead lifeline system for horizontal fall protection in industrial applications
Overhead lifeline systems provide essential fall protection for workers operating in areas where traditional guardrails or other fall protection methods are not practical. This comprehensive guide covers design, installation, and maintenance of overhead lifeline systems for various industrial applications.
Understanding Overhead Lifeline Systems
An overhead lifeline system is a horizontal fall protection system installed above the work area, allowing workers to move freely while maintaining continuous connection to the lifeline. These systems are particularly valuable in environments where work areas change frequently or where permanent fall protection is not feasible.
Types of Overhead Lifeline Systems
1. Flexible Overhead Systems
- Wire Rope Systems: Most common type using galvanized steel cables
- Synthetic Webbing Systems: Lightweight alternatives for temporary applications
- Adjustable Systems: Allow for easy reconfiguration of work areas
2. Rigid Overhead Systems
- Beam Systems: Utilize existing structural beams as anchor points
- Track Systems: Dedicated tracks for trolley-based connections
- Monorail Systems: Single rail systems for linear work areas
3. Portable Overhead Systems
- Tripod Systems: Self-supporting portable units
- Davit Systems: Adjustable portable anchor points
- Mobile Gantry Systems: Wheeled systems for changing work locations
Key System Components
Structural Components:
- Anchor points and brackets
- Horizontal lifeline (cable or beam)
- Intermediate supports
- Tensioning devices
- End terminations
- Energy absorbers
Connection Hardware:
- Trolleys or shuttle devices
- Carabiners and connectors
- Self-retracting lanyards
- Shock absorbing lanyards
- Full body harnesses
Design Considerations and Requirements
Structural Requirements
Critical Design Factors:
- Load Capacity: Minimum 22 kN (5,000 lbs) per attached worker
- Safety Factor: 2:1 minimum for all components
- Deflection Limits: Maximum sag under load conditions
- Swing Clearance: Minimum 2.5 meters in all directions
- Maximum Span: Typically 18-30 meters depending on system type
Environmental Considerations
- Corrosion Protection: Galvanized or stainless steel components
- Temperature Range: Material performance in extreme conditions
- Wind Loading: Additional loads from wind and weather
- Chemical Exposure: Compatibility with industrial environments
Installation Process and Best Practices
Pre-Installation Planning
- Site Survey: Assess work area and identify hazards
- Structural Analysis: Verify anchor point capacity
- System Design: Engineer system for specific application
- Permit Acquisition: Obtain necessary work permits
- Material Procurement: Source certified components
Installation Steps
Phase 1: Anchor Installation
- Mark anchor point locations
- Drill holes to specifications
- Install anchor bolts or brackets
- Torque to manufacturer specifications
- Conduct pull tests
Phase 2: Lifeline Installation
- Install end terminations
- Route lifeline through supports
- Apply proper tension
- Install intermediate supports
- Conduct system testing
Safety Standards and Compliance
Indian Regulatory Requirements
Standard/Act | Requirement | Application |
---|---|---|
IS 3521 | Construction safety code | Building construction sites |
IS 15871 | Personal fall protection | All fall protection systems |
Factory Act 1948 | Workplace safety provisions | Industrial facilities |
Contract Labour Act | Contractor safety requirements | Contract work sites |
International Standards
- ANSI Z359: American fall protection standards
- EN 795: European anchor point standards
- CSA Z259: Canadian fall protection standards
- AS/NZS 1891: Australian/New Zealand standards
System Applications by Industry
Manufacturing
- Assembly line work
- Equipment maintenance
- Warehouse operations
- Quality control access
Construction
- Precast installation
- Steel erection
- Roofing work
- Facade installation
Infrastructure
- Bridge maintenance
- Tunnel work
- Airport operations
- Stadium maintenance
Maintenance and Inspection Protocols
Daily Pre-Use Inspection
- Visual inspection of all components
- Check anchor point integrity
- Verify lifeline tension and condition
- Test trolley or shuttle operation
- Inspect personal protective equipment
- Check clearance areas
Periodic Maintenance Schedule
Interval | Maintenance Activity | Responsible Party |
---|---|---|
Weekly | Detailed component inspection | Competent person |
Monthly | Lubrication and cleaning | Maintenance technician |
Quarterly | Tension adjustment and testing | Qualified engineer |
Annually | Complete system overhaul | Certified inspector |
Troubleshooting Common Issues
Causes: Insufficient tension, overloaded span, worn components
Solutions: Adjust tensioning device, add intermediate supports, replace worn parts
Causes: Dirt accumulation, insufficient lubrication, worn bearings
Solutions: Clean system, apply appropriate lubricant, replace worn components
Causes: Vibration, thermal cycling, inadequate initial installation
Solutions: Re-torque connections, use thread locker, install vibration dampeners
Training and Certification Requirements
User Training Program
Basic User Training (4 hours)
- System overview and components
- Proper connection procedures
- Pre-use inspection requirements
- Emergency procedures
- Hands-on practice
Advanced Training (8 hours)
- System design principles
- Installation procedures
- Maintenance requirements
- Troubleshooting techniques
- Rescue procedures
Cost-Benefit Analysis
Initial Investment Considerations
- System Cost: ₹50,000 - ₹200,000 per installation
- Installation: ₹15,000 - ₹50,000 depending on complexity
- Training: ₹5,000 - ₹10,000 per worker
- Annual Maintenance: 5-10% of initial system cost
Return on Investment
- Accident Prevention: Avoid injury costs and downtime
- Insurance Savings: Reduced premiums for improved safety
- Productivity Gains: Faster, safer work completion
- Compliance Benefits: Avoid regulatory penalties
Pro Tip:
Consider modular systems that can be reconfigured for different applications. This flexibility maximizes your investment and adapts to changing work requirements.
Future Trends and Innovations
- Smart Systems: IoT sensors for real-time monitoring
- Lightweight Materials: Advanced composites and alloys
- Automated Installation: Drone-assisted installation techniques
- Predictive Maintenance: AI-powered maintenance scheduling
Conclusion
Overhead lifeline systems represent a crucial investment in workplace safety, offering flexible fall protection solutions for diverse industrial applications. Proper design, installation, and maintenance ensure reliable protection while maximizing system lifespan and performance.
Expert Overhead Lifeline Solutions
HSSPL offers comprehensive overhead lifeline system services including design consultation, installation, training, and ongoing maintenance support. Our certified engineers ensure optimal system performance and regulatory compliance.
Get Professional Consultation