Horizontal Lifeline System Installation & Components Guide - Complete Safety Setup
June 26, 2025
HSSPL Safety Experts
12 min read
Comprehensive guide to horizontal lifeline systems for rooftop and industrial safety. Learn about installation, components, standards, and maintenance requirements.
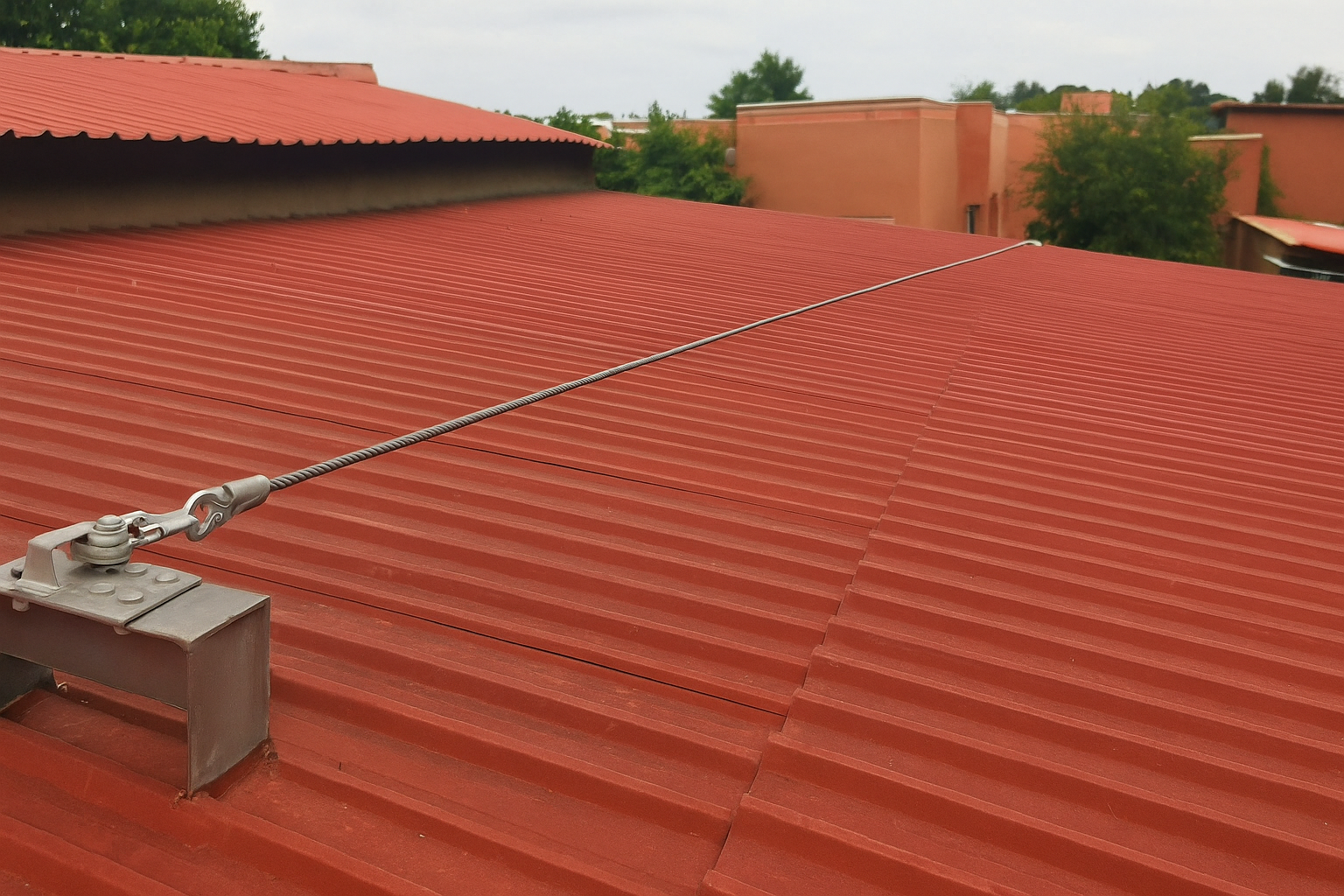
Horizontal lifeline system installation for rooftop and industrial safety
What is a Horizontal Lifeline System?
A horizontal lifeline system (HLS) is a fall protection system that allows workers to move horizontally while remaining connected to a secure anchor line. It's essential for rooftop work, construction, and maintenance activities where workers need mobility along a horizontal path.
Key Benefit: Provides 100% tie-off protection while allowing full horizontal movement across work areas.
System Components
Anchor Components
- End Anchors: Terminal anchor points
- Intermediate Anchors: Support points every 15-20m
- Corner Units: Direction change points
- Tensioner: Cable tension adjustment
Connection Hardware
- Wire Rope: 8mm-12mm stainless steel
- Traveler/Glider: Mobile connection point
- Shock Absorber: Energy absorption device
- Carabiners: Connection hardware
Installation Planning
Structural Assessment
Before installation, conduct thorough structural analysis:
- Load Calculations: Minimum 22kN per user, factor in dynamic loads
- Span Limitations: Maximum 30m between intermediate anchors
- Deflection Analysis: Cable sag should not exceed safety clearance
- Environmental Factors: Wind loads, temperature variations
Design Considerations
Parameter | Requirement | Standard Reference | Notes |
---|---|---|---|
Cable Strength | Minimum 36kN breaking load | EN 795, IS 3521 | Stainless steel 316 grade preferred |
Anchor Strength | 22kN per connected user | EN 795 Class C | Include safety factor 2.5:1 |
Clearance Below | Minimum 2.5m | EN 363 | Includes fall distance + safety margin |
Span Length | Maximum 30m | EN 795 | Intermediate supports required beyond |
Step-by-Step Installation Process
Phase 1: Site Preparation
Phase 2: Anchor Installation
- End Anchors: Install at designated termination points with proper reinforcement
- Intermediate Supports: Position every 15-20m to limit cable deflection
- Corner Units: Install at direction changes with appropriate angular calculations
- Load Testing: Proof test each anchor to 150% of design load
Phase 3: Cable Installation
- Cable Routing: Thread wire rope through all anchor points
- Tensioning: Apply initial tension using calibrated tensioner
- Final Adjustment: Set working tension to manufacturer specifications
- End Connections: Secure cable ends with proper terminations
⚠️ Critical Safety Notes
- Never exceed maximum span lengths without engineering analysis
- Ensure proper fall clearance calculations including pendulum swing
- Use only certified components meeting EN 795 or equivalent standards
- Install systems only by trained and certified personnel
- Conduct annual inspections and recertification
Maintenance Requirements
Daily Visual Inspection
- Check cable for cuts, kinks, or corrosion
- Verify anchor point integrity
- Inspect travelers and hardware for damage
- Ensure proper cable tension
Monthly Detailed Inspection
- Measure cable tension with calibrated gauge
- Check all connection points for looseness
- Inspect shock absorbers for deployment indicators
- Document all findings in maintenance log
Annual Certification
- Complete system recertification by qualified engineer
- Load testing of critical components
- Cable replacement if wear limits exceeded
- Update system documentation and certificates
Common Applications
Industrial Rooftops
- HVAC maintenance access
- Solar panel installation
- Roof inspection routes
- Emergency egress paths
Construction Sites
- Leading edge protection
- Facade work platforms
- Bridge construction
- High-rise building work
Specialized Applications
- Airport maintenance
- Stadium facilities
- Ship building yards
- Power transmission lines
🌟 HSSPL Horizontal Lifeline Solutions
HSSPL offers complete horizontal lifeline systems designed and manufactured to international standards:
- Custom engineered solutions for any application
- IS 3521 and EN 795 certified components
- Professional installation and commissioning services
- Comprehensive maintenance and inspection programs
- 24/7 technical support and emergency response